Robotics Researcher: Specialty Crops to Drive Technology Adoption in Farming
#Recipe #Foody
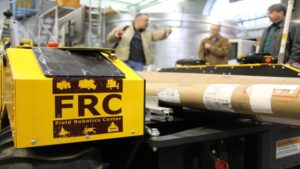
Carnegie Mellon University professor and researcher George Kantor (background left) discusses some of his recent work around applying robotics concepts in specialty crops while Meister Media Worldwide Executive Editors Richard Jones (middle) and Paul Schrimpf (right) look on.
Carnegie Mellon University researcher George Kantor, slated to deliver one of the keynotes at this week’s Washington State Tree Fruit Association Annual Meeting in Wenatchee, WA, sees producers of high value specialty crops largely driving the robotics in ag revolution, at least early on.
“The apple industry in Washington, their consortium is really good and the growers are really forward-looking, and it’s really well organized,” the tenured professor told us during a recent visit to the Pittsburgh, PA, campus. “And then it’s the same way with grape growers.”
The overall burgeoning cost of labor, as well as a shrinking pool from which to find workers, are two significant factors that lead the internationally renowned developer of robotics to see the path forward for robots in ag in this manner.
“And, I mean, it’s not like these farmers are being cheap and don’t want to pay,” Kantor adds. “They’re actually paying $20 an hour and they still can’t get people. It’s kind of miserable work, and nobody wants to do it.
“And there’s so much risk for the grower, if the labor doesn’t show up, at harvest time all of those dollars are hanging on the trees.”
Grower Size Matters
Kantor, whose group of grad students and colleagues are currently working on commercializing a between the rows, RGB-imaging robot for tree fruit health scans, believes the early adopters of ag robots in specialty crops will likely be the larger, more sophisticated operations that have been planning on this type of shift change for years now.
“If you look at some of these innovations, it’s about more than just the cost of the machine,” he says. “If you look at the Abundant Robotics apple harvester, for example. They have strict requirements on what the tree canopy has to look like. The trellis system and how the trees are pruned, all of that must be to specification, or the machine won’t work. So, it becomes a question of not just who can afford the machine, but who can afford to have that growing system and who can execute it?
“The growers that were forward-looking ten years ago and started planning and building some of these super precise trellis architectures for other business reasons, those growers are in really good shape for when the robotic harvesters come in,” Kantor adds. “And the growers that decided to keep their big bushy, 3-D canopies, those growers are going to have to replant or risk going out of business.”
Another interesting Kantor tidbit from the visit: the researcher believes the agricultural robot that will truly transform growing will be something that can work autonomously and tackle multiple tasks around the farm, such as a field robot that could conceivably spray, harvest, prune, and variable rate inputs. Current iterations purposely-built with only one farm task in mind, like the robotic lettuce thinners and harvesters on the market, are great early-stage applications of the technology. But the next wave will have multiple capabilities built into one system.
Message to Growers: Get Moving!
Speaking with Kantor in his CMU research lab, he had a clear message to deliver to growers interested in implementing robotics on the farm: What are you waiting for?
“I plan on telling those (Washington tree fruit) growers ‘Here’s what’s coming (with robotics) and here’s what you have to do to prepare for it’,” he says. “It’s not like you can just sit back and wait for these things to show up at the farm gate. Technology doesn’t just magically appear out of thin air and start solving problems.”
As an example, Kantor points to the incredibly manual task of harvesting wine grapes today, the bulk of which happens in California, a state with a high minimum wage requirement and cutthroat competition for labor in the ag sector.
“Today we have a robot that can take the grape cluster off the vine, but we’re not quite there yet on having the robot do the cluster cleaning task,” he says. “If you look at just the idea of replacing the people in the field and the way they do things now, that’s like a 50-year goal. You need the level of dexterity that humans possess in their fingers in a robot, and we’re not even close to that.
“But, if you think about having the robot take the cluster off the vine, and then automatically transporting the clusters into an air-conditioned, indoor lit facility and then having the people do that step in there, then it starts to make sense, right?”
That sort of push-and-pull dance between the developers of new technologies for ag, and those actively in the field doing the work today, is exactly what the industry needs to make sure the innovations it brings to market are useful to the grower.
“A grower has to look at new tech and say ‘Yeah, I’ll take the risk in changing my whole process, which has been developed over decades and works really well for me right now, to try to anticipate this risky idea going forward’,” Kantor explains. “What’s going to happen is one grower will try it (new technologies) and either fail or succeed, and if they succeed other growers will follow that. But there’s got to be this kind of active engagement in the technology from the grower side for it to work.”
A Quick Plug for PrecisionAg Vision Conference
Kantor will also be presenting the latest on his research at Carnegie Mellon with attendees of Meister Media Worldwide’s upcoming PrecisionAg Vision Conference, held January 14-16, 2020, in Seattle, WA. For more information and to register for the event, head on over to thevisionconference.com.
Matthew J. Grassi is the Technology Editor for Greenhouse Grower and American Vegetable Grower, both Meister Media Worldwide brands. See all author stories here.
Recipe
via https://www.DMT.NEWS
Matt Grassi, Khareem Sudlow
- Share:
0 comments